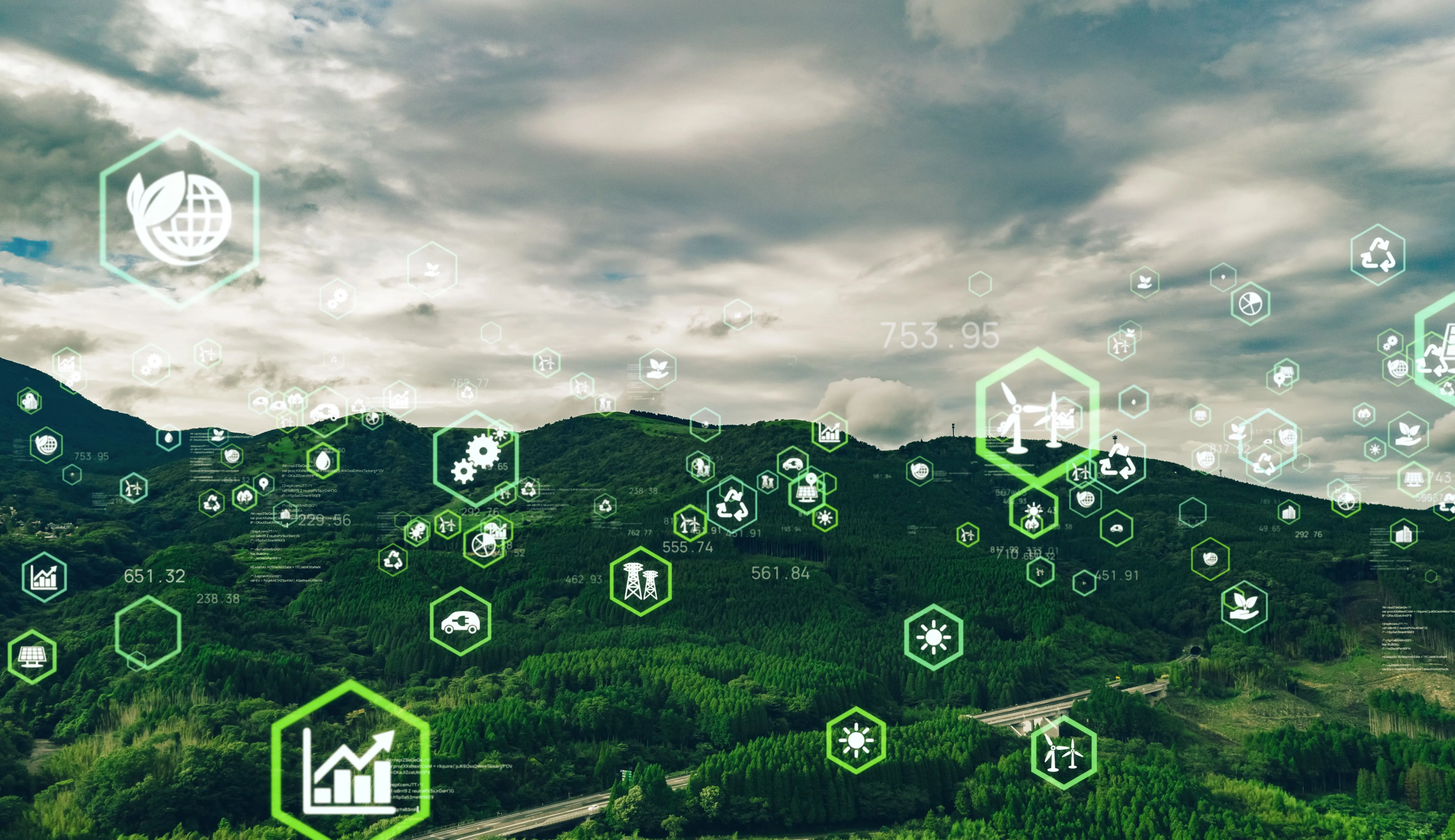
Global green hydrogen just got real with Ohmium’s India gigafactory
The gigafactory will supply green hydrogen solutions to our customers across the globe, including current projects in the United States, Europe, and the United Arab Emirates.
On July 19, India’s newest proton exchange membrane (PEM) electrolyzer gigafactory opened its doors in the city of Doddaballapura near Bangalore in southern India. This marks an important milestone towards cost-effective green hydrogen and a big step forward on the world’s path to decarbonization.
Under the Paris Agreement, countries agreed to limit global temperature rise to 1.5°C above pre-industrial levels. Reducing greenhouse gas (GHG) emissions is by far the most important way to achieve that goal.
While renewable energy allows us to cut emissions from much of our economy, renewables can’t cut emissions from everything. That’s because many industries — like steel, cement, fertilizer, chemicals and refineries — all use gray or brown hydrogen. That is, hydrogen made from fossil fuels. In order to decarbonize these industries, we must decarbonize the hydrogen that they use. For example, if we want our steel to be green, the hydrogen used to make it must to be green.
Green hydrogen is one of the key pillars, along with renewables, to achieve that 1.5°C goal.
PEM Technology
Ohmium’s new gigafactory mass produces PEM electrolyzers. Electrolyzers are a kind of electrochemical cell that use electricity to split water molecules — H2O — into their constituent parts of oxygen and hydrogen. This process is called water electrolysis. When this process is powered by renewable energy, the resulting product is known as green hydrogen.
We manufacture cutting-edge PEM technology electrolyzers at the gigafactory, the very same technology used by NASA and in other aerospace applications. Experts consider PEM technology to be a superior choice because it’s very efficient, very energy dense, and pairs better with renewables than any other electrolyzer technology.
However, conventional wisdom says PEM technology won’t be cost-effective and commercially viable until around 2040.
The Ohmium Advantage
We’re happy to say that this conventional wisdom is wrong. We make PEM cost effective with alkaline technology (a common kind of electrolysis technology) today.
How do we do this? To put it simply, we mass produce fully assembled hyper modular electrolyzer units. Let’s unpack that by first examining why mass production is so important.
Mass producing electrolyzers enables the lowest possible production cost, at the highest possible quality. Our gigafactory has an initial capacity of 2 gigawatts (GW) per year, capable of abating 4 million tons of CO2 annually. That’s the equivalent of 180 million trees or pulling over 850,000 cars off the road for a year!
But the benefits go beyond cost and quality. Factory capacity can be scaled up much more quickly than with the custom engineered products typical in the industry. At Ohmium, we can double the production of the gigafactory to 4 GW in less than 2 years. And that means that even more forward-thinking steel producers, energy suppliers, chemical refineries, fertilizer producers — the list goes on and on — can cost-effectively decarbonize their operations and their products.
Now let’s dive a little deeper into our unique, hyper modular design.
Ohmium’s cutting-edge PEM technology is so energy dense that we were able to design our electrolyzers to be around the size of a car. This hyper modular design has many benefits, one of the key ones being ease of installation.
Across the industry installation costs are typically as much as CAPEX, but with Ohmium, installation costs are only 10-20% of CAPEX. We assemble complete electrolyzer units at the gigafactory and deliver them to our customers’ sites. Once they are connected to electricity and water, the units are ready for hydrogen production. This makes installation fast and easy, cutting installation costs by 80-90%. And for those sites where there’s very little available land, we can actually install electrolyzer modules vertically, that is, stacked on top of each other. That keeps the cost of land — and the total project cost — low.
There are many other benefits to our hyper modular design, but one is especially worth noting — lower technical risk. With our hyper modular design, each additional unit actually reduces system risk: if one hundred units make up the installation, a single unit failure decreases production by only 1%. That’s why Ohmium has the highest availability of any electrolyzer solution.
Benefits across the Globe
According to BloombergNEF, clean hydrogen supply is expected to skyrocket 30-fold by 2030 and that still won’t be enough to meet government targets. We are poised to play a key role in that growth.
The gigafactory will supply green hydrogen solutions to our customers across the globe, including current projects in the United States, Europe, and the United Arab Emirates.
We’re also here to help our customers achieve their goals and provide them with a competitive advantage. With the gigafactory and our hyper modular solution, they can get going quickly — from equipment arrival to commissioning in as little as 3 weeks — and with the right amount of green hydrogen production capacity for their particular needs. Add in guaranteed hydrogen production, remote monitoring, and lifetime equipment maintenance, and it’s easy to see why more customers are choosing Ohmium than ever before.
Have a question about our products? Need a quote? Contact the Ohmium team today.
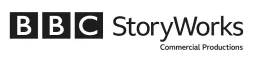
